Steel making is a very old process and has contributed to development of technological societies since ancient times. The previous stage to steelmaking is the ironmaking process, which is performed inside blast furnace. Blast furnace is a metallurgical reactor used to produce hot metal (95% Fe, 4.5%C) from iron ore. The burden contains iron ore, fluxes and coke. The process involves an exothermic reaction, the gasification of carbon. High temperature inside the blast furnace is required to increase the gasification of carbon. The temperature in the hearth can be as high as 1500 degree Celsius. The thermal stresses induced by high temperature inside the blast furnace hearth limit the overall blast furnace campaign period. The numerical computation of thermal stresses requires coupling of thermal and mechanical models and solve the associated coupled system.
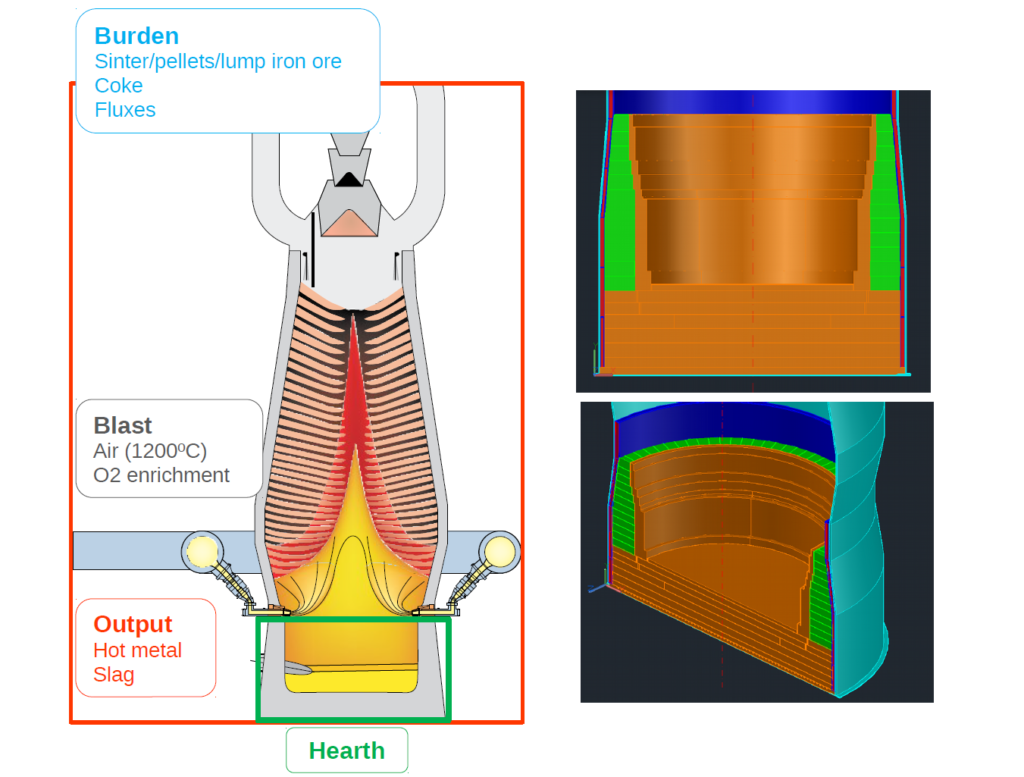
My work in this project has two main objectives. First objective is to numerically compute temperature profile inside the blast furnace hearth walls and compute thermal stresses. This requires application of concepts from the field of continuum mechanics, numerical analysis and scientific computing. However, the increasing demand of these fields for complex processes has put computational resources under considerable pressure. This is particularly true if such computations are required to be performed repeatedly at different parameters. By parameters, we mean variations in the material properties or in the geometry of the domain of interest. In the absence of efficient computational algorithms, the simulations might be time consuming, if not unfeasible, with available computational power. Hence, another objective of my work is to make the computations faster and efficient while maintaining reliability of numerical simulation above minimum acceptable level by using techniques of reduced order modeling for parametric partial differential equations.
Interdisciplinary nature of this project brings additional challenges. While working with the industrial partner, inputs about the processes from experienced professionals in the field of blast furnace operations and experimental measurements are gathered. During the analysis work, mathematical methodologies are devised under supervision of experts in the field of continuum mechanics, applied mathematics and scientific computing. It can be quite challenging sometimes to coordinate and bring everyone at the common platform. This challenge has motivated me to develop skills in various fields in order to be capable of working with experts from different domains. Besides, an industrial doctorate in the ROMSOC project framework has provided me environment to be disciplined as a professional as well as flexible and open minded as a researcher. In addition to the skills obtained within an individual project, the training courses and networking opportunities have contributed significantly by providing overview of concepts in other potentially relevant areas and in turn, have helped to gain alternative perspective about research.
I am confident that the learning process will continue further and I look forward to positively contribute to the organizations involved and at large, to the scientific community.
About the author:
Nirav Vasant Shah is an Early-Stage Researcher (ESR10) within the ROMSOC project. He is a PhD student at the Scuola Internazionale Superiore di Studi Avanzati di Trieste (SISSA) in Trieste (Italy). He is working in collaboration with ArcelorMittal, the world’s leading steel and mining company, in Asturias (Spain) and Technological Institute for Industrial Mathematics (ITMATI) in Santiago de Compostela (Spain) on the mathematical modelling of thermo-mechanical phenomena arising in blast furnace hearth with application of model reduction techniques.”