Most of the steel we use every day comes from continuous casting. This is a process which was first introduced in the 1950s, but the first patents are hundred years older. Before continuous casting, the steel was poured into closed molds to form ingots. With the development of continuous caster became possible to produce continuous billet, blooms or slabs. It allowed to have very long pieces with better quality, much faster. The thecnology has improved since its invevention and nowadays these casters can produce up to 10 meters of steel per minute.
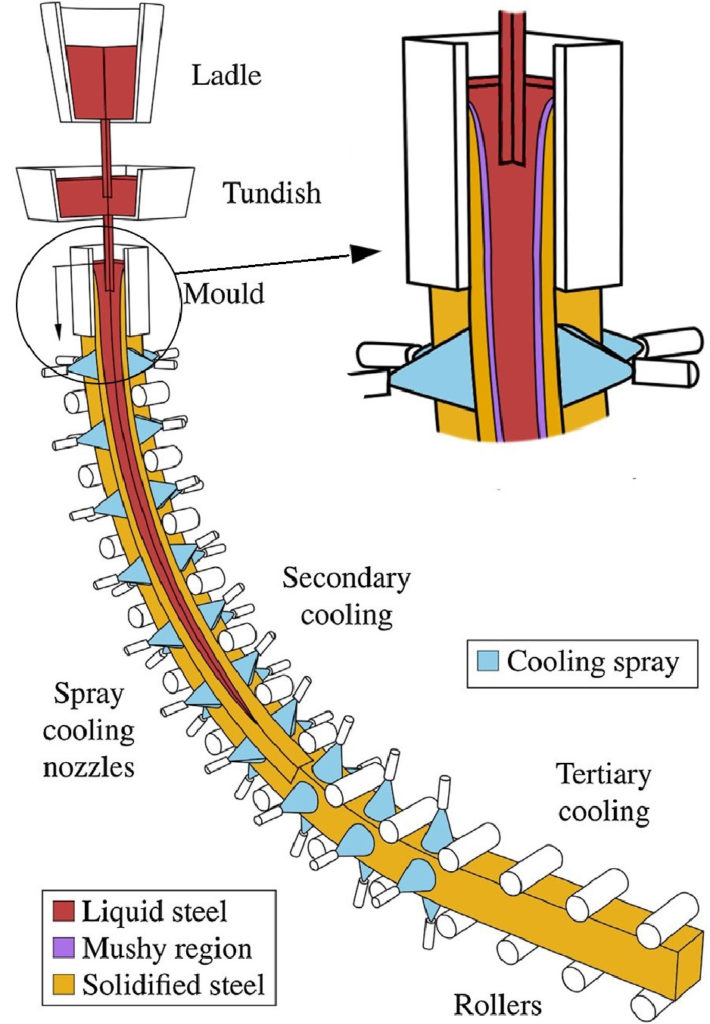
The industrial partner of this project is the Italian steelmaking company Danieli & C. Officine Meccaniche SpA, they design and run continuous casters. According to the ROMSOC DNA, Danieli came up with the challenge. As these casters go faster and faster, to control the quality of the product becomes harder and harder. The main problems arise in the mold. There the steel begins its solidification and external imperfections can appear due to a wrong heat extraction from the mold which is cooling down the steel.

Until now, steelmakers used thermocouples to measure the temperature at some points in the mold. This in not sufficient for a proper understanding of the behavior of the mold because what we are really interested in is the heat flux between the mold an the solidifying steel. Then, the objective of my project is to develop a method for estimating the heat flux at the boundary of the mold based on the measurements of the thermocouples made inside the mold domain. Moreover, this has to be done in real time. This problem is what we call an inverse problem. As you may know, it ain’t easy to work with inverse problems which, by the way, are ill-posed. Several techniques are available for solving this kind of problem however they are generally computationally expensive. Here is where Model Order Reduction (MOR) comes into the picture. In my project, we want to exploit MOR to speed up the solution of this inverse heat transfer problem obtaining real time computations of the heat flux. After this brief overview of the subject of my PhD, in the next posts I will go deeper in the methodology we are developing. So keep visiting the ROMSOC blog to stay updated with mine and all other terrific projects.
About the author
Umberto Emil Morelli is an early stage researcher within ROMSOC. He is doing his PhD in reduced order modeling for boundary conditions estimation in heat transfer problems at the Technological Institute for Industrial Mathematics (ITMATI) in collaboration with Danieli & C. Officine Meccaniche SpA and the Scuola Internazionale Superiore di Studi Avanzati (SISSA).
One Reply to “Continuous casting – Modern techniques to solve an old industrial problem”
Comments are closed.